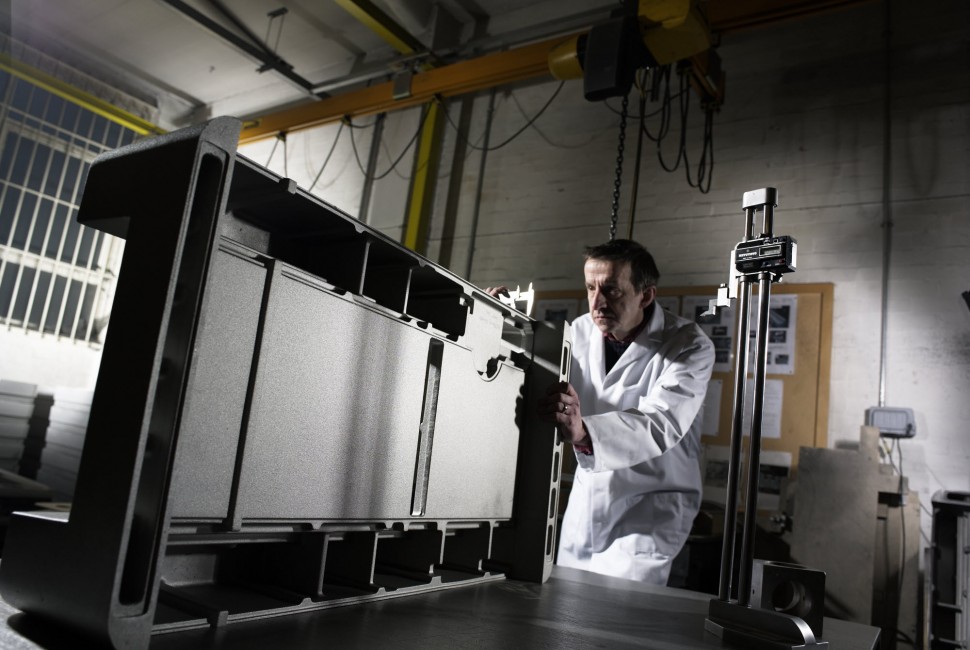
Inspection of an oncology couch casting
The type of casting testing and casting inspection methods we might use may vary depending on the size and complexity of the project. However, our onsite laboratory is fully equipped to carry out an impressive range of casting testing and inspection techniques.
As part of our ongoing commitment to quality control, we are committed to continuously analysing our mechanical processes, our sand compositions, and our alloys. In this way, we are able to abandon any inefficient processes that result in lower quality castings, whilst further developing any processes that lead to higher yields and superior metallurgical properties.
Our casting inspection and analysis is complimented by our extensive metal control process, which incorporates spectrographic analysis, density indexing, and rotary degassing. (During the aluminium casting process, it is possible for pockets of hydrogen to spread through the molten metal. As not all sections of the casting solidify at the same rate, there is a risk that this hydrogen will remain, resulting in a low quality, porous castings).
Density indexing is a process by which we test for and reduce the porousness of our castings. We subject a sample of molten aluminium to a reduced pressure test (RPT), where it is allowed to solidify in a vacuum. The reduced pressure enhances the size of the porosity formed.
Comparing this sample to a sample that was allowed to solidify under atmospheric pressure allows us to calculate the density index of the molten aluminium, which can be regarded as a measure of its cleanliness.
We draw from this information to improve the efficiency and the effectiveness of the subsequent degassing process. For this, we use a technique called rotary degassing. This involves making use of gasses such as nitrogen in order to eliminate the presence of hydrogen in the molten aluminium, resulting in stronger, more durable castings.
As part of our commitment to stringent ISO 9001:2015 quality regulations, every casting project we undertake is submitted to an intensive process of testing and inspection.
Harrison Castings Ltd offer an approved casting testing and inspection services including:
- Real Time Radiography
- Film Radiography
- Dye Penetration
- Helium Gas Leakage Testing
- Hydraulic Testing
- Impregnation
- Mechanical Analysis
- Chemical Testing
- Pressure Testing – up to 2000 kPa or 290 psi.