This 15ft diameter, four tonne aluminum wheel was made in our Gough Road foundry in 1953.
This would be impressive in itself. But what’s even more remarkable is that we managed to cast one of our largest ever casting without the advanced techniques we use today.
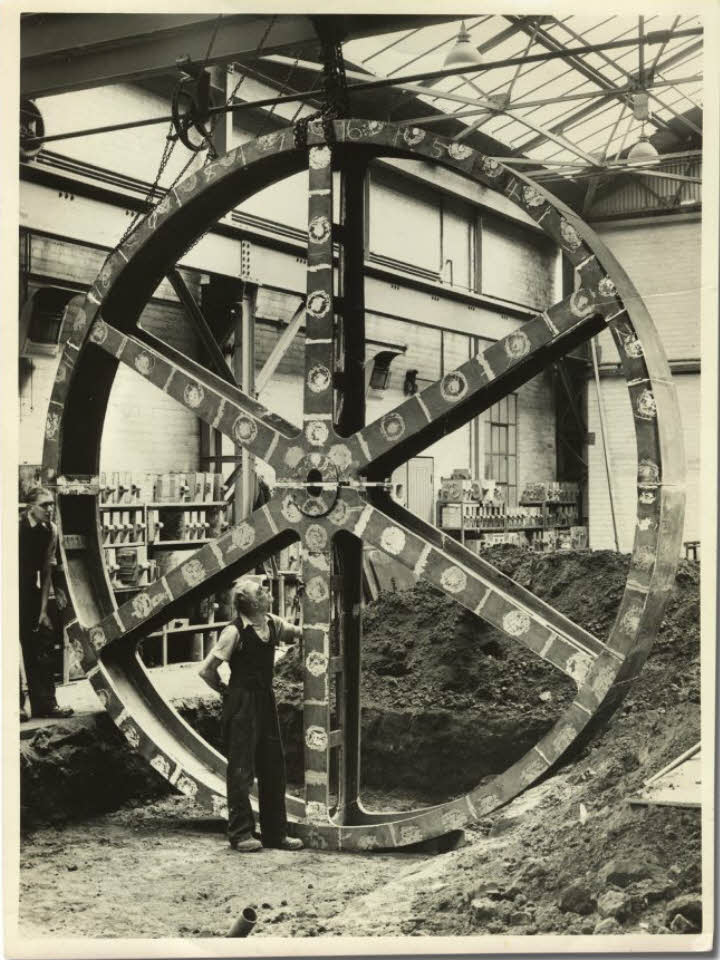
The 15ft diameter, 4 tonne aluminum wheel made for Dunlop of Leicester
These days, at Harrison Castings, we use the air set sand casting technique. This is a process that makes use of molds made from dry sand bonded with a fast curing adhesive resin.
There are many benefits to using the air set sand casting technique, the main one being that the process produces a very strong mold that’s capable of standing by itself, free of any molding boxes. As a result, there is technically no limit to the size of an air set casting mold, which frees us to create castings in any size necessary.
But when making our largest ever casting, we had to rely on the old green sand casting technique. It was 1953, after all!
Green Sand Casting
Traditional green sand casting involves the use of wet sand in the creation of casting molds. It did not involve sand that was “green” in colour. Rather, the term “green” indicates that the sand was used in a wet state.
The “sand” used in the green sand casting process was actually a mixture of olivine sand, clay, water, and small amounts of minerals and other inert materials. The water activated the bonding qualities of the clay, binding the sand together. When packed around patterns, this created a mold that was strong enough to allow for the pouring of molten metal, producing a casting.
Obviously, we had to use a lot of sand when building the mold for our 15ft, four tonne aluminum wheel. But one of the main benefits of the green sand casting process was that it was so cost-effective. Up to 95% of the sand used could be reclaimed and reused afterwards.
Also, green sand casting molds, whilst tough, were not strong enough to stand by themselves. Instead, they required the support of a molding box. As a result, the larger the casting, the greater the challenge.
This aluminum wheel therefore acted as an undeniable testament to our foundry’s capabilities. Needless to say, Dunlop were very pleased!
And if we can successfully cast one of the largest aluminum castings of all time using the green sand casting technique, imagine what we can do with the air set technique…